Refractory Silicon Carbide (SiC): The Unyielding Guardian of Extreme Heat
In the blistering heart of industrial furnaces, where temperatures rage beyond 2000°C and molten metals flow like liquid fire, Refractory Silicon Carbide (SiC) stands as an indomitable sentinel. Born from the alchemy of silica and carbon in electric furnaces, this engineered ceramic emerges with a crystalline defiance—boasting a melting point of 2830°C, thermal conductivity rivaling copper (120–170 W/m·K), and a hardness eclipsed only by diamond. Unlike traditional refractories that crumble under thermal shock, SiC thrives in the chaos of rapid heating and cooling, its covalent Si-C bonds unshaken even after 1,200+ thermal cycles (ASTM C1525).
When molten steel roars at 1600°C, SiC steps into the inferno as both protector and performer. As furnace linings in electric arc furnaces (EAFs), it slashes energy use by 15–20%—its high thermal conductivity ensuring even heat distribution. In ladles and tundishes, it resists not just heat but the corrosive siege of molten slag (basicity index >2.5) and metal splatter. The secret? A self-armoring SiO₂ layer (Wagner oxidation kinetics) that thickens at 1200°C, outlasting graphite by a factor of ten.
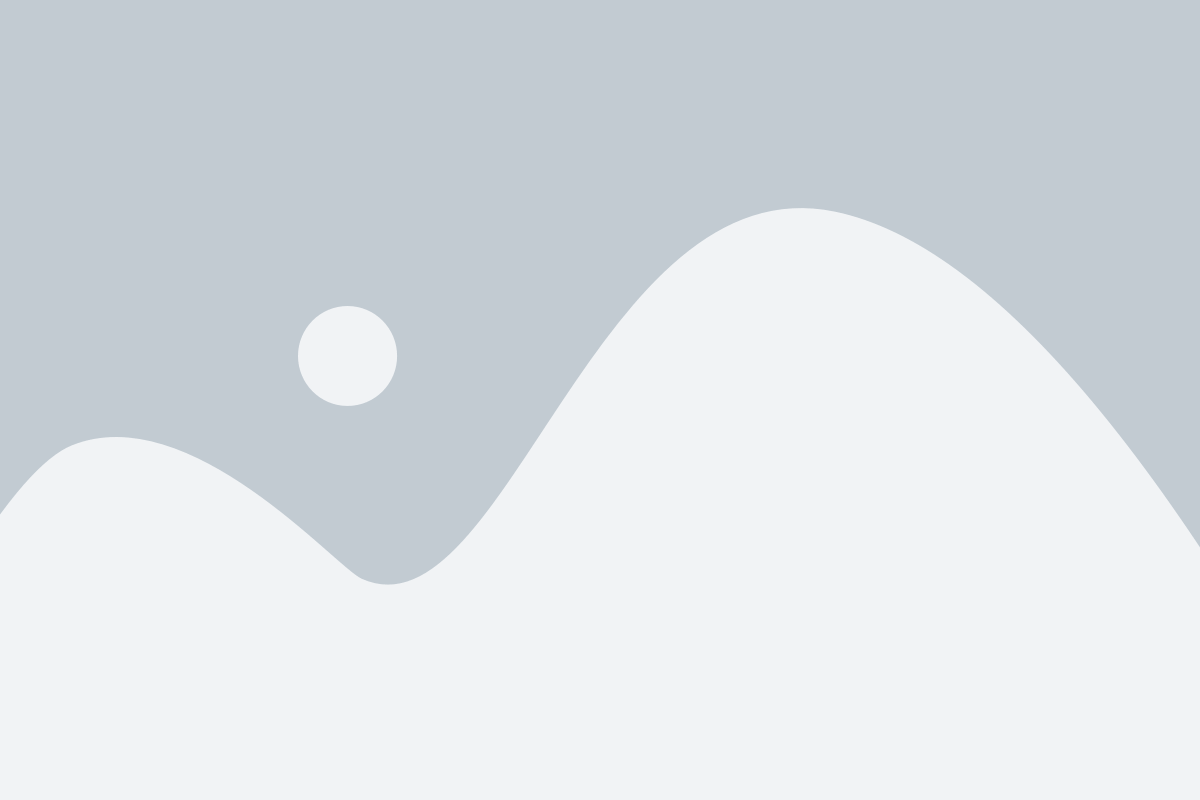
Beyond Metallurgy: Conquering Corrosion and Wear
SiC’s reign extends to cement kilns and glass tanks, where alkali vapors (Na₂O, K₂O) dissolve lesser materials. Here, its chemical inertness (corrosion rate <0.01 g/cm²·h in NaOH at 800°C) and 10⁻⁷ mm³/N·m wear rate make it the champion of longevity. In aerospace, it shields rocket nozzles from 3000°C exhaust plumes, while in semiconductors, its wide bandgap (3.2 eV) enables devices to operate where silicon fails.
Visual Pairing: Slow-motion video of molten glass flowing over an SiC kiln roller, with an inset microscope view of its untouched surface.
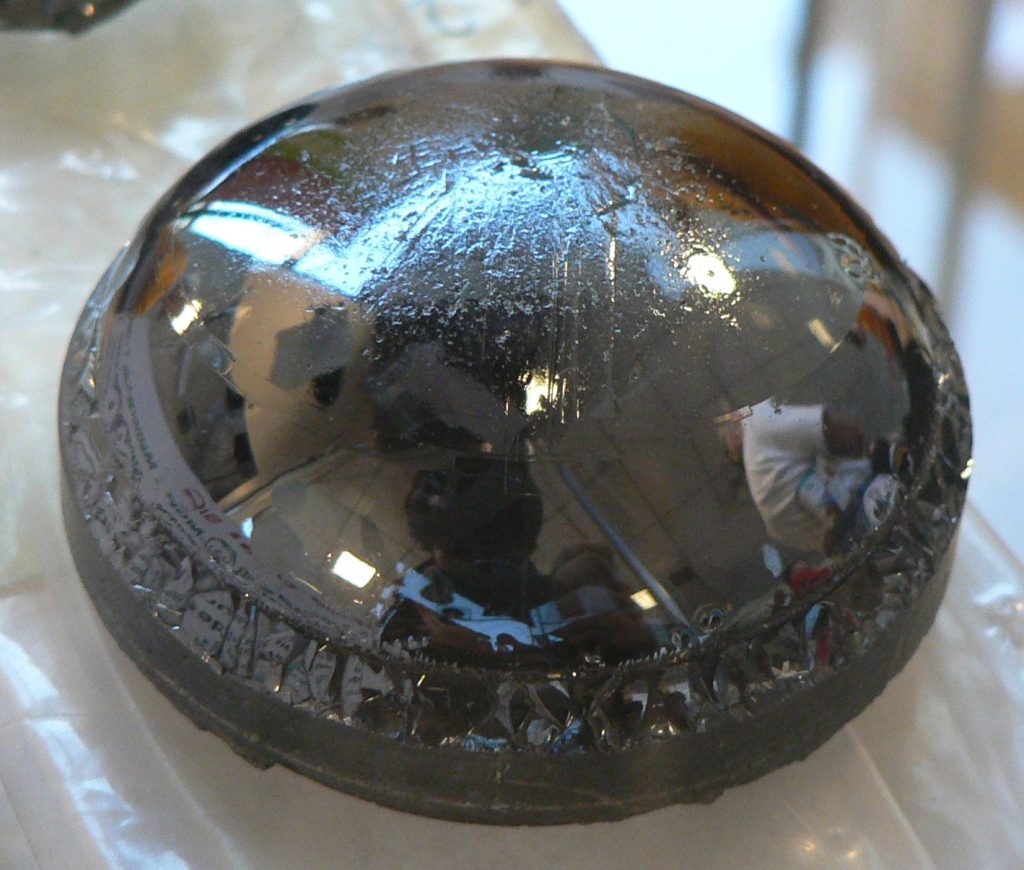
Faraed Pouya’s Engineering Mastery
At Faraed Pouya, we push SiC’s limits through nitride-bonded SiC (NBSiC) technology, achieving 99.5% density with fracture toughness of 4.5 MPa·m¹/²—perfect for rotary calciner linings that endure 200+ thermal shocks daily. Our data sheets reveal the granular science: grain boundary engineering with Al₂O₃ sintering aids, pore size distribution <5 µm, and CTE matching zirconia. The result? Refractories that don’t just survive, but redefine endurance.