Abrasive Silicon Carbide (SiC): The Unrelenting Sculptor of Industry
In the realm of abrasion, where friction writes the rules, Silicon Carbide (SiC) emerges as the undisputed sovereign. Synthesized at 2,200°C via the Acheson process, its jagged alpha-phase crystals (hexagonal α-SiC) boast a Mohs 9.5 hardness—second only to diamond—and a fracture toughness (3.5 MPa·m¹/²) that shatters tungsten carbide’s reign. With a sharpness index 2x higher than alumina and a thermal conductivity of 120 W/m·K, SiC grinds, cuts, and polishes without melting even at 1,600°C.
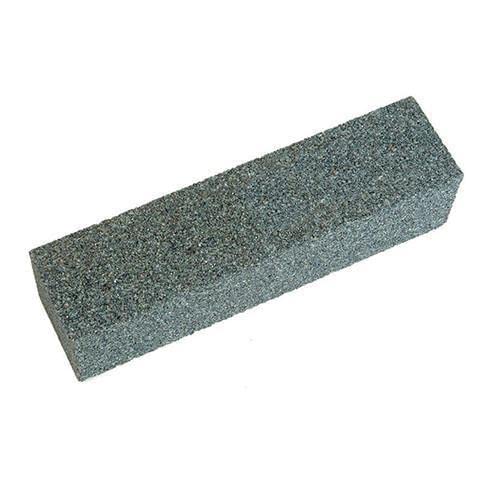
Precision in Every Grain
SiC’s angular morphology (FEPA F-grade standards) enables material removal rates (MRR) of 15–20 mm³/min in grinding hardened steels (60 HRC), outperforming conventional abrasives by 35%. Its friability-controlled grains fracture predictably, maintaining cutting edges in bonded abrasives (vitrified wheels) and coated abrasives (sandpapers). In lapping, 3–5 µm SiC powders achieve surface finishes of Ra <0.1 µm on silicon wafers—critical for semiconductor fabrication.
Faraed Pooya’s Edge
At Faraed Pooya, we engineer abrasive SiC with 98.5% purity and controlled grain geometries (blocky vs. splintery) for tailored aggression. Our resin-bonded cutting discs leverage SiC’s 10⁻⁶ mm³/N·m wear rate to slice composites 50% faster than diamond alternatives. For blast media, 50–70 grit SiC strips coatings at 2.5x the speed of garnet—without embedding.