Calcined Petroleum Coke (CPC) The Carbon Backbone of Modern Industry
In the searing crucibles of rotary kilns, Calcined Petroleum Coke (CPC) is born—a metamorphosed carbon engineered to perfection. Green petroleum coke, a byproduct of crude oil refining, undergoes calcination at 1,200–1,350°C, shedding 8–12% volatile matter (VM) and emerging with 98–99.5% fixed carbon. Its crystalline structure transitions to an ordered graphitic lattice, achieving electrical resistivity as low as 450–550 µΩ·m—a critical trait for aluminum smelting anodes. With sulfur content crushed to <3.0% and trace metals (V, Ni) below 300 ppm, CPC becomes the silent architect of conductivity and purity.
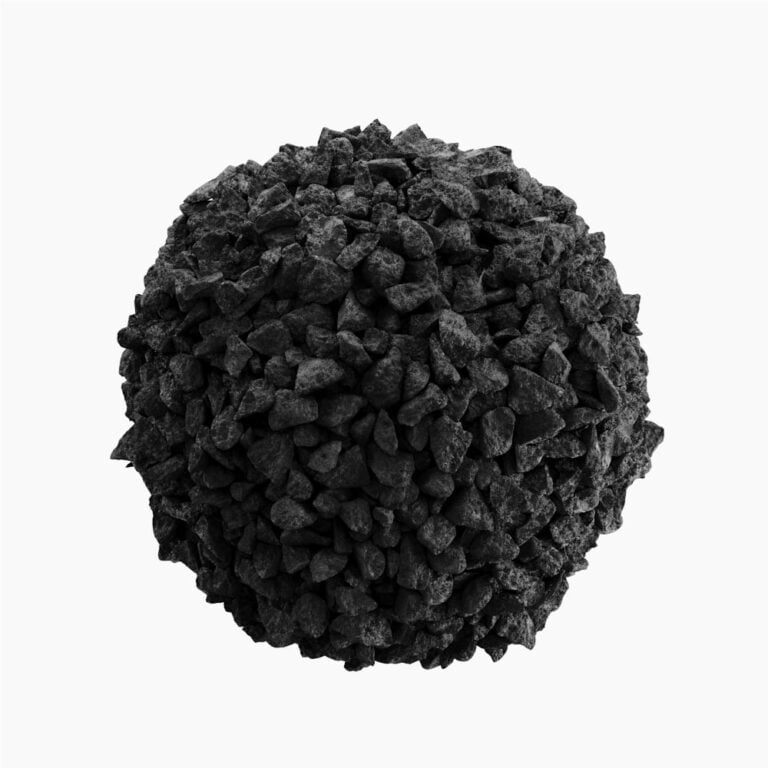
Powering Aluminum’s Electric Heart
In Hall-Héroult cells, where 12–15 kA currents rip through molten cryolite, CPC-based anodes withstand 950°C thermal assaults while maintaining CO₂ reactivity <25 mg/cm²·h. Each metric ton of aluminum consumes 400–450 kg CPC, its low ash (<0.5%) preventing slag contamination. Beyond smelting, CPC’s 22–28% porosity and 0.5–1.5 mm particle size optimize titanium dioxide production in chloride process reactors, where Cl₂ purity hinges on carbon’s impurity lockdown.
Steel’s Carbon Cavalry
As a recarburizer in electric arc furnaces (EAFs), CPC injects 90–95% carbon yield into molten steel, outperforming coal tar pitch by 15–20% efficiency. Its 1.8–2.2 g/cm³ bulk density ensures controlled dissolution, while <0.1% moisture eliminates hydrogen pickup. In graphite electrodes, CPC’s CTE of 2.5–3.5×10⁻⁶/K (vs. 4.5×10⁻⁶/K for needle coke) resists cracking under 2,800°C arc temperatures, extending electrode life by 30%.
Faraed Pouya’s Calcination Mastery
At Faraed Pouya, we refine CPC through indirect-fired rotary kilns with AI-driven O₂ control, achieving 99.2% fixed carbon and <2.5% sulfur consistently. Our particle size distribution (PSD) optimization ensures D50 = 12–18 µm for anode blocks vs. D90 < 75 µm for recarburizers. Coupled with XRF-certified impurity profiles, our CPC powers industries where carbon is not just a element—it’s a precision tool.