Synthetic Graphite: The Engineered Conductor of Extreme Environments
Forged in the crucible of advanced thermochemical synthesis, synthetic graphite transcends its natural counterpart through precision engineering. Via the Acheson process (2,500–3,000°C) or CVD deposition, its turbostratic layers achieve >99.9% carbon purity with a crystallographic orientation index (OI) of 0.85–0.95. This yields a material boasting 2.5–5.0 µΩ·m electrical resistivity, 150–400 W/m·K thermal conductivity, and flexural strength up to 80 MPa—properties fine-tuned for industries where carbon is not just an element, but a performance catalyst.
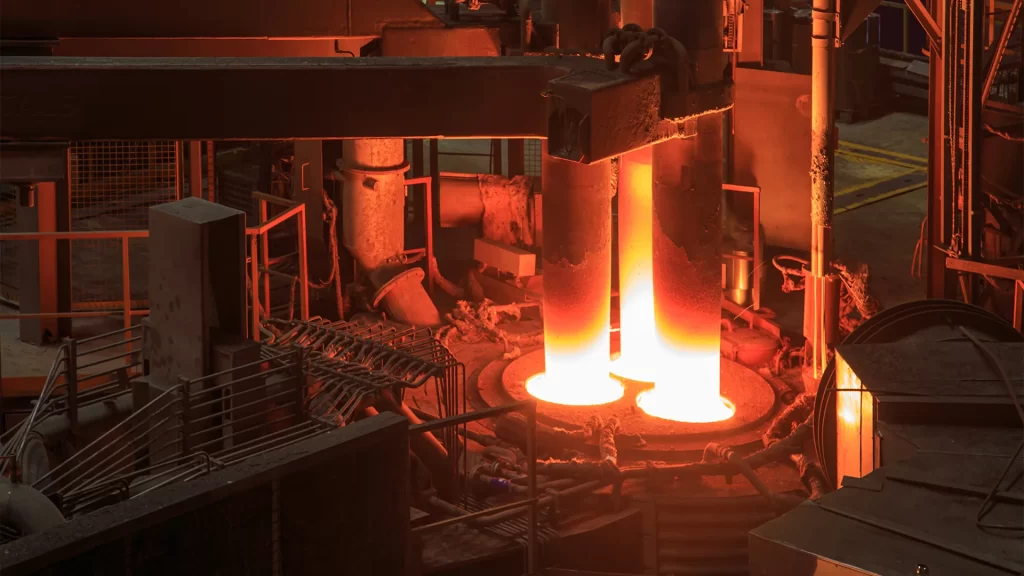
Metallurgy’s Silent Conductor
In electric arc furnaces (EAFs), synthetic graphite electrodes channel 50–150 kA currents at 1,600–2,000°C, degrading at <0.5 kg/ton steel—half the wear rate of amorphous carbon. Its isotropic structure (CTE: 1.5–4.5×10⁻⁶/K) resists thermal shock during >1,000 melt cycles, while <50 ppm sulfur prevents steel contamination. As recarburizers, 1–5 mm granules deliver 95–98% carbon yield, outperforming petroleum coke by 20% efficiency in ultra-low-carbon steel refining.
Aerospace & Energy: Conquering Extremes
Synthetic graphite thrives where others fail: rocket nozzle throats endure 3,500°C hypersonic flows (ablation rate: 0.1 mm/s), while fuel cell bipolar plates leverage <10 mΩ·cm² contact resistance at 80–90% RH. In lithium-ion anodes, its 372 mAh/g theoretical capacity and >500 cycle stability enable EVs to surpass 500 km/charge. Even in semiconductor epitaxy, 10–20 ppb impurity levels ensure defect-free SiC wafer growth.
Faraed Pooya’s Mastery
At Faraed Pooya, we engineer synthetic graphite with AI-optimized grain alignment (Raman ID/IG ratio <0.15) and nano-SiC doping to push flexural strength to 120 MPa. Our isostatic pressing technique achieves 1.80 g/cm³ density with <5 µm pore size, while XRD-certified crystallinity guarantees performance. From 800 mm-diameter EAF electrodes to 0.1 mm-thick fuel cell foils, we redefine carbon’s limits.